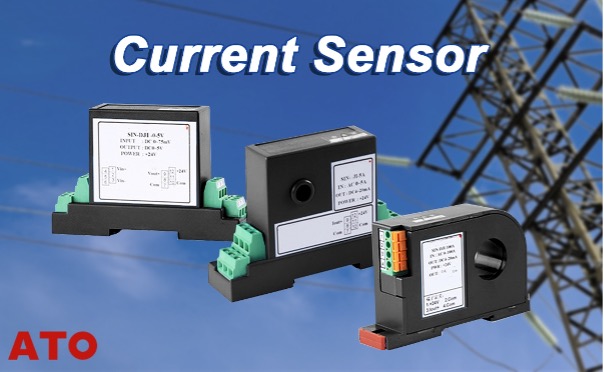
5 Tips For Choosing A Current Sensor
Confused about selecting the right current sensor for your needs? Choosing a current sensor is a hard row to hoe, especially with hundreds to pick from! How do you choose the right current sensor when there are so many to choose from? If you know the criteria for your application, you can narrow down the options for sensors.
It is crucial to be able to measure current in a system without compromising its functionality. In many instrumentation and power systems, current measurement is thus crucial. Historically, current sensing has served primarily as a safety and regulation mechanism. However, with the development of technology, current sensing has emerged as a method to analyze and enhance efficiency. Knowing the total amount of current being delivered to the load is useful in a wide range of contexts. This article provides an overview of a modern sensor and its types. Later, we’ll put the spotlight on a few factors buying the best sensor for you. So, let’s dive in!
What Is A Current Sensor?
Current sensors are devices used to sense and convert the current to a measurable voltage. This voltage is directly proportional to the total current across the route being measured. The resulting voltage signal may be read by an ammeter, utilised as a control input, or saved for further analysis in a data gathering system. So this is what a current sensor is for.
There is a wide variety of sensors on the market, and each one serves a unique purpose in terms of the kinds of environmental and climatic variables it can detect. By inserting a resistor into the current channel, a current sensor may be thought of as a current-to-voltage converter, allowing the current to be converted into voltage in a linear fashion. This sensor’s technology is noteworthy due to the fact that different sensors may be tailored to certain tasks.
How Does A Current Sensor Function?
A current sensor detects changes in electrical current by measuring the resulting voltage drop and magnetic field produced close to the conductor carrying the current. Therefore, there are two types of current sensing: direct and indirect.
You can click here to learn more about power analysis, which delves deeper into how current sensors play a critical role in energy monitoring, system diagnostics, and performance optimization. Understanding these principles is essential for designing efficient and safe electrical systems.
Ohm’s law is the backbone of direct sensing, whereas Ampere’s and Faraday’s laws are essential for indirect sensing. Voltage loss due to current flow in passive electrical components may be measured using direct sensing. In a similar vein, the magnetic field close to a current-carrying wire may be measured by indirect sensing. The generated magnetic field is then put to use in generating a current proportionate to the voltage, which is then transformed for further measurement or control applications.
Types Of Current Sensors
Today’s sensors come in a wide variety of forms, including wireless, analog, and digital. Depending on the sort of perk, they are put to use as sensors. These sensors will be used to continually monitor the current values of different appliances and machinery. The current standard sensor types for a wide variety of measurements include:
1. Shunt Resistor
DC current is often measured with a shunt resistor current sensor. The shunt resistor works on the idea that when a DC current is sent through a resistor, a voltage will be generated across it. The key advantages of these sensors are cheap cost, rapid reaction time, and high accuracy, whereas the main disadvantage is that the measuring circuit is not electrically separated from the current flow. This method is suitable for measuring low-frequency currents with tiny amplitudes.
2. Hall Effect Current Sensors
The Hall effect and Ampere’s law provide the basis for the construction of the Hall current sensor. These sensors can detect alternating currents (AC) and direct currents (DC) up to 100 kilohertz in frequency. These sensors rely on a Hall effect device at their heart and on signal conditioning circuitry to process the data they collect. They operate on the principle of the Hall Effect, according to which a magnetic field is generated whenever current runs through a conductor.
Electrons will be redirected to one side of the conductor if it is placed in another magnetic field, since the magnetic field created by the conductor will interact with the external magnetic field. As a result, a voltage will be generated that is directly proportionate to the amount of current passing through it. These sensors’ key advantages are their isolation and accuracy, but their disadvantage is their sluggish effect speed. The benefits include great accuracy and excellent isolation, while the drawbacks are a sluggish rate of influence and an inaccuracy in measuring tiny currents.
3. Current Transformer
The electromagnetic induction principle underlies the operation of a current transformer, also known as a current sensor. The primary goal here is to reduce the magnitude of the original current so that it can be measured and protected against. The iron core and the windings are the main parts of a current transformer. With the safety circuit and measuring device simply coupled in series, the secondary winding of this device has a greater number of turns than the primary winding, which is wired in series with the current line to be detected. Once this transformer begins operating, its secondary circuit will remain closed at all times, resulting in an exceptionally low series coil impedance for use in the protection circuit and measurement device.
4. Fluxgate Current Sensor
The fluxgate current sensor is structurally identical to a Hall element-based current sensor, except that it employs a magnetic probe coil in lieu of the Hall element. This sensor is perfect for most high-precision medical and industrial devices since it can monitor current from 6 to 600A. These sensors are ideal in fast-moving mechanical systems due to their robust construction, high resolution, capacity to sense a broad variety of weak magnetic fields, and ability to directly measure magnetic field components.
How To Choose A Current Sensor
There are so many things to consider when deciding on your current sensor. For your convenience, a variety of current sensors are available at ATO.com, a reliable industrial automation components supplier. Everything is brand new, with a full guarantee. They provide the most effective solutions to problems facing businesses throughout the world, and ATO Inc has developed into a cutting-edge, fast-response distributor of automation technologies. Let’s look into the following major things to choose the best current sensor.
1. Select The Right Measurement Range
Current sensors have a certain range of current that may be measured with high precision; this range is called their measurement range. It’s crucial to choose a sensor with a suitable measuring range for the task at hand. Overloading the sensor is a risk if the range is too high, while measuring the complete range of current is impossible if the range is too low. The sensor’s resolution, or the smallest current change it can detect, is also crucial.
2. Care About the Sensor’s Precision or Linearity
Selecting a current sensor requires thinking about its accuracy and linearity. The linearity of a sensor is its ability to retain a consistent sensitivity over its measurement range, while its accuracy is how closely its readings match the real values. To guarantee precise and trustworthy readings, a sensor with good accuracy and linearity should be used.
3. Look Into the Sensor’s Response Time
The time it takes for a sensor to register a change in current and generate an appropriate output signal is known as its “response time.” Selecting a sensor with a quick reaction time guarantees precise and timely readings. If the reaction time is too long, the sensor or circuit might be damaged in situations where the current is constantly shifting.
4. Consider the Sensor’s Specific Installation Instructions
When choosing a current sensor, it is also crucial to think about the installation requirements. While some sensors must be permanently installed, others may be surface-mounted on a PCB. Check to ensure the sensor you choose can be mounted where you want it to. It’s also crucial to think about the sensor’s orientation, since some of them are more sensitive in one way than another.
5. Test The Current Flow
Checking the accuracy of the sensors requires verifying their responses in real time. If the sensor data are accurate, then the sensors are utilised to track how much power the motor is receiving. If one of our motors is receiving insufficient or excessive current, we may adjust the chassis accordingly. This evaluation is used to verify the reliability of current sensors from previous generations. These sensors need to be checked for functionality because of the past short-circuiting. For successful device evaluation and measurement, these sensors must function as intended.
The Crux Of The Matter!
Getting precise and trustworthy readings requires picking the correct current sensor. Ato is ready to lend a hand and provide you with high-quality products that enhance your business and daily lives.
There are several factors to think about when choosing a current sensor, including the sensor type, measurement range, precision, linearity, reaction time, and installation needs. The aforementioned factors will help you select the current sensor that is best for your requirements and obtain accurate results.